PLC timing and debugging tools
When analyzing relay control logic or analog circuit, only the relationship between signals needs to be considered, and the sequence is rarely considered. In these systems, the signal propagates at the speed of light, and the results will take effect immediately, and the results will be fed back to the front end for processing.
However, for PLC, its core is a CPU. Like all computers, the execution of program instructions is in sequence and is scanned repeatedly. In the process of one scan, the subsequent results cannot be used by the previous program immediately, and must wait until the next scan to be effective. Therefore, when compiling PLC programs, especially complex logic, there must be a clear concept of time sequence (time sequence is the meaning of time sequence). When learning PLC, time sequence is an important content.
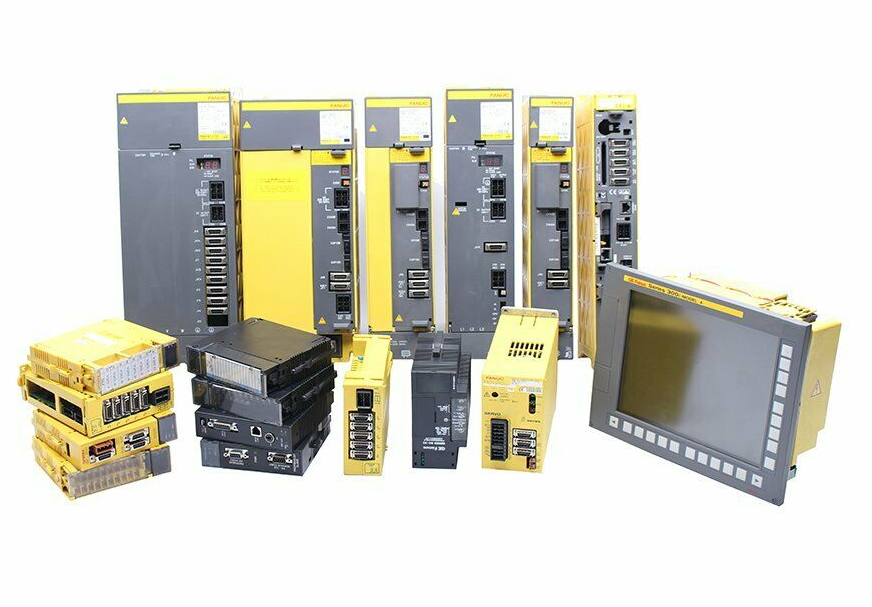
Take an example of automatic control of drainage pump (only I / O points related to automatic control are given). Its working principle is that there are two switch signals of low level and high level (both are detected by float switch. When the float is raised, the signal is high level, and when the float is lowered, the signal is low level). The output is the signal of pump startup. The ladder diagram in the PLC can realize the functions of high liquid level start and low liquid level stop with only a simple program. The logic and working sequence of the ladder diagram shall first use PLC programming software for PLC debugging. These programming software can monitor the status of each variable and program diagram. This is a basic function, otherwise it cannot be debugged. For most slow and simple logic, the basic functions of the programming software are sufficient to complete the debugging task.
However, if the logic is complex, spans many pages, or the signal changes very quickly, it is very difficult to observe the real-time state with the naked eye and think logically. Most of the programming software will provide a variable monitoring table to put all the variables that need to be concerned into. Click monitoring to refresh the status in real time. This can solve the problem of monitoring a large number of variables to a certain extent. However, for complex logic or fast changing programs, it is necessary to record the change process with the help of the tool of sequence diagram and analyze it slowly afterwards.
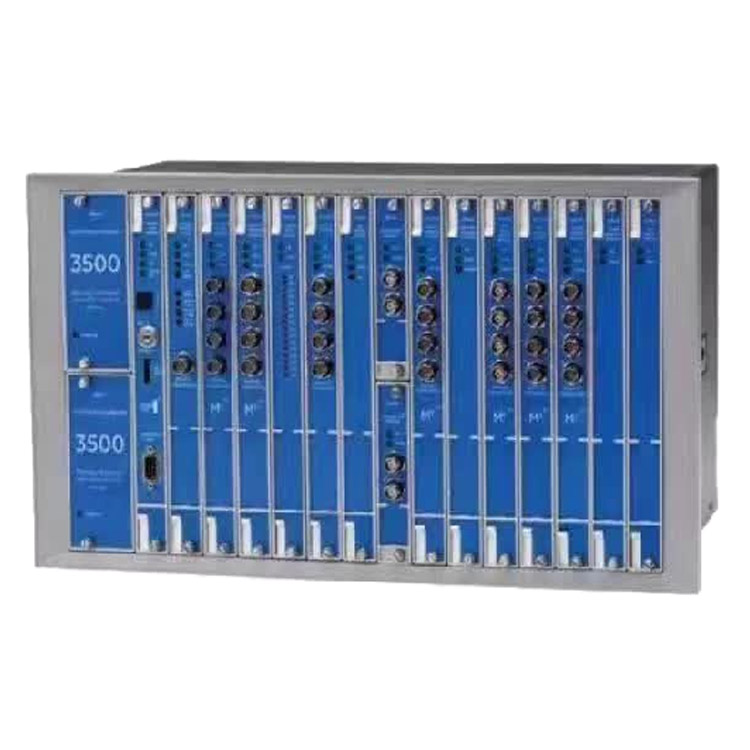
In the simple example of pump control above, if a phenomenon is encountered, the pump will occasionally stop before reaching the low liquid level after starting, what is the reason? It may be the jitter of the low liquid level signal, or the loose wiring of the output. At this time, it is easy to judge if the timing chart can be obtained. If the sequence diagram is shown in Fig. 2, we can judge that the low level signal is unreliable, and check the wiring of the low level signal or the float switch. If the sequence diagram is shown in Figure 3, it is necessary to check the output wiring of the control command and the main circuit of the motor. In addition to program debugging and troubleshooting, the wave recording software can also be used to record the data concerned by the user for subsequent analysis, such as recording the current curve of the motor and observing whether the startup process is normal. Record the flow, pressure and other process parameters to check whether the production is stable, whether the sensor is normal, and whether the performance of the closed-loop controller is appropriate. If the recorded data is related to production rhythm, it can be exported for analysis of production efficiency and control process.
www.plc-module.com
XiongBa industrial control,PLC-Module,Automation,DCS System
Small editor:Panda