DCS and PLC points of difference
1 DCS is a "decentralized control system", and PLC (programmable controller) is just a control "device", the two is the difference between "system" and "device". The system can realize the function and coordination of any device, PLC device only realizes the function of this unit.
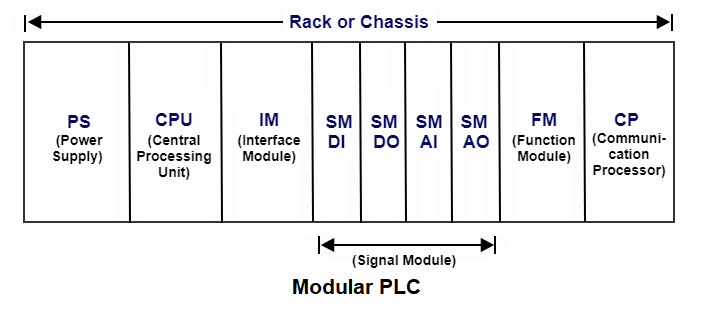
2. In terms of network, DCS network is the central nervous system of the whole system, it is a safe and reliable double redundancy high-speed communication network, the system's expansion and openness is better. And PLC because basically all work for the individual, its in communication with other PLC or upper computer, the network form is basically a single network structure, network protocol is often inconsistent with international standards. In network security, PLC does not have very good protection measures. We use dual redundancy of power supply, CPU and network.
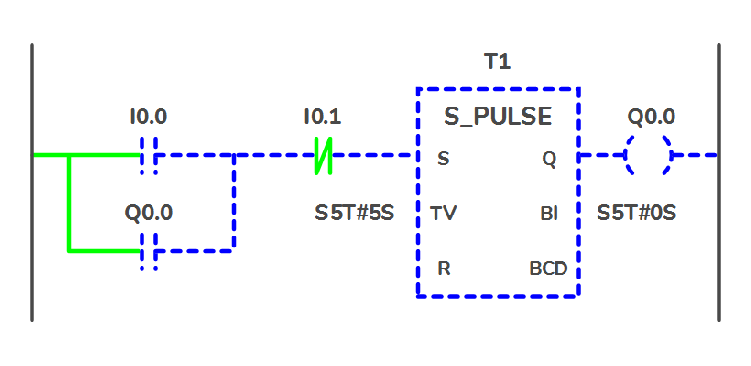
3. DCS overall consideration of the scheme, the operator station has the function of the engineer station, station and station in the operation of the program after installation is a close association between any station, any function, any controlled device is interlocking control, coordination control; And the single use of PLC connected with each other constitute the system, the station and station (PLC and PLC) between the connection is a loose connection, is not a coordinated control function.
4. DCS in the whole design has a large number of extensible interface, external system or extension system is very convenient, PLC lapped after the completion of the whole system, want to arbitrarily increase or reduce operator station is difficult to achieve.
5. DCS security: in order to ensure the safety and reliability of the DCS control equipment, DCS uses a double redundant control unit, when the important control unit failure, there will be related to the redundancy unit real-time no interference switch to the work unit, to ensure the safety and reliability of the whole system. The PLC lapped system basically does not have the concept of redundancy, let alone redundant control strategy. Especially when a PLC unit failure, have to stop the whole system, can be replaced and maintenance and need to be reprogrammed. So the DCS system than its safety and reliability on a higher level.
6. System software, the various process control scheme update is one of the most basic functions of DCS, when a scheme changes, the engineer only need to change the scheme compiled in the engineer station, execute the lower command can, the lower process is automatically completed by the system, does not affect the original control scheme operation. All kinds of control software and algorithms can improve the control precision of process control object. For in the composition of PLC system, very large workload, you first need to determine which is to edit update by PLC, and then to use the program compiled with the matching compiler, final reoccupy special machine (read-write) special one-on-one to send the PLC program, during the system debugging, and debugging cost a huge increase in debugging time, And extremely detrimental to future maintenance. The control accuracy is far from the same. This determines why in large and medium-sized control projects (more than 500 points), basically do not use all the PLC connected to the system.
More...
PLC-Module.com | XiongBa Industrial Control | Panda | DCS and PLC points of difference |