Computer control system for industrial boiler
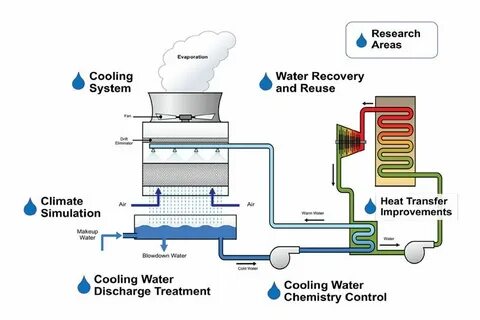

1、In the combustion process of industrial boilers,all technical indicators are required to be limited within a certain range.In order to ensure the stable,reliable and economic operation of the combustion process,advanced frequency conversion speed regulation technology and computer application technology are adopted in the design,and the boiler combustion process computer automatic control device.The device controls the rotating speed of the drum,induced draft fan and grate through the computer and frequency converter by detecting the water vapor pressure,temperature,furnace negative pressure and other operating physical quantities,changing the volume of the drum,induced draft fan and coal feed,so that the furnace negative pressure,drum water level and temperature are controlled within the predetermined range,and the boiler combustion is guaranteed to operate under the best working conditions and the most energy-saving conditions.The most prominent feature of this unit is to solve the problem that the boiler heat load and output can not be matched in time,that is,the steam demand and steam supply can not be well matched,the steam supply is small or large,which can not meet the change of heat demand at any time,and the steam supply quality is poor.At present,this problem is mainly regulated by manual experience,and the manual control is basically always a large steam supply,with a large waste of heat.The traditional problem that the steam supply lags behind the furnace temperature change,which is most difficult to solve,is successfully solved by combining computer application technology,expert intelligence system and partial micro fractional analog conversion calculation of thermal mathematics.The device can adjust the steam supply quantity in real time to achieve accurate steam supply.
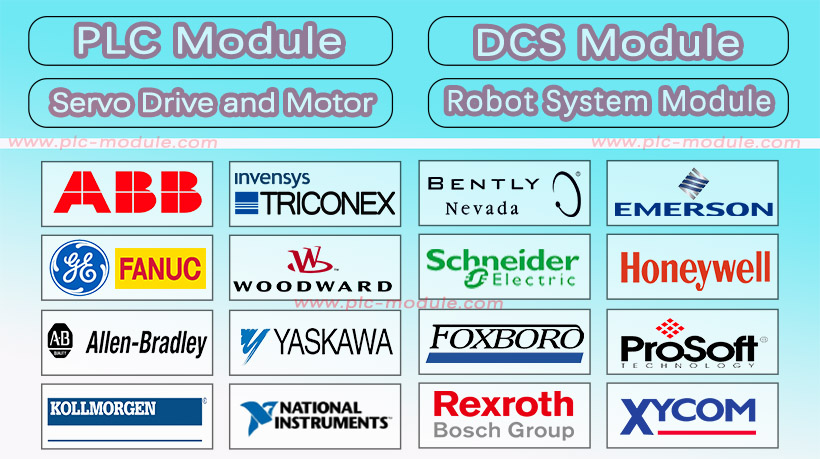
2、Control Assumption The frequency conversion speed regulation computer automatic control device of the steam boiler combustion system combines the frequency conversion speed regulation technology,the computer and the intelligent control technology to complete the automatic control of the industrial boiler on the parameters such as water supply,coal supply,air supply,and induced air,so that the boiler drum water level,steam pressure,steam flow,and air coal ratio are under the control of the expert system to achieve the self optimizing control of the combustion conditions and maintain the best operating state of the boiler.Realize the safe,reliable and stable operation of industrial boiler system and achieve the purpose of energy saving and consumption reduction.
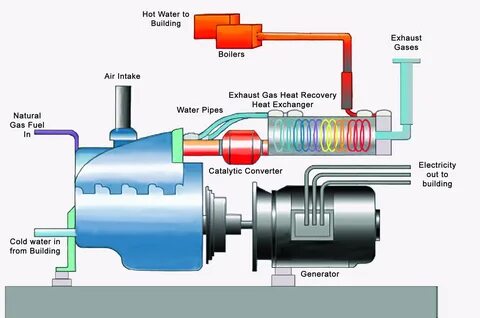
The boiler combustion system is a complex multivariable coupling system.Input quantity includes:coal feeding quantity,air blowing quantity and induced air quantity;Output:steam pressure,furnace negative pressure.Fuel is the only source of heat.The change of coal feed directly affects the steam provided by the boiler,and also affects the change of steam drum pressure.It is the main control quantity of the combustion system.The change of air blowing volume will produce different air coal ratio and corresponding combustion conditions,show different furnace temperatures,determine the size of furnace loss,and directly determine whether the boiler can operate economically.When the air supply volume changes,the air supply volume also changes,so as to keep the furnace negative pressure stable and ensure the safe operation of the boiler.These three control sub loops form an integral whole,which is collectively called the boiler combustion control system to jointly ensure the flexibility,economy and safety of the boiler operation.The combustion process of boiler is a complex physical process,and the coupling relationship between input and output is very complex;The boiler system has a large time delay,and the parameters change in real time,so it is difficult to establish an accurate mathematical model;The load of the boiler varies from zero to the maximum load,and the load varies from time to time.Conventional PID is difficult to control.The method to solve these problems is to adopt a more effective intelligent control technology than PID-fuzzy control method.In this control system,artificial intelligence is introduced into the control scheme.The main steam pressure control adopts the idea of fuzzy control to overcome the characteristics of time-varying and large delay of the steam pressure controlled object,and maintain the main steam pressure regulating system with constant drum pressure with fuel quantity;In order to ensure the economic combustion of the boiler,the air supply volume control adopts the self optimizing control to maintain the economic combustion of the air supply regulation system;The furnace negative pressure is controlled by PID,and the furnace negative pressure regulating system maintains the stability of furnace negative pressure with induced air volume.The basic fuzzy control of main steam pressure lacks the control ability for the object with large pure time delay.Therefore,SMITH predictive control is introduced into the fuzzy control system to improve the control ability of the fuzzy controller for the object with pure time delay.The commonly used fuzzy controller link has two forms:proportional output and integral output.The former has fast step response,but is a differential control.The latter can approach the zero error control,but has slow response and large overshoot.The system adopts the proportional integral output structure combining the two,which has the advantages of small overshoot and short transient time.Fuzzy control algorithm has the characteristics of fast step response,high accuracy,insensitivity to parameter changes and easier tuning,which fully reflects the good adaptability of intelligent control method to the object.
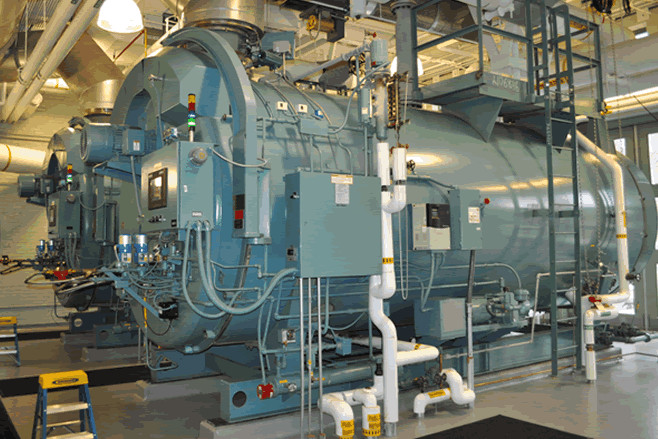
The SMITH prediction is introduced into the fuzzy controller,which improves the control ability of the control system to the object with pure time delay.The fuzzy SMITH control is much better than the conventional SMITH control in terms of both the rapidity of control and the adaptability to parameter changes.There are many operating parameters affecting the boiler combustion system,and it is difficult to establish an accurate mathematical model due to the existence of pure time delay.Therefore,the use of self optimizing control that belongs to the category of adaptive control in theory,but does not need to establish an accurate mathematical model.At present,the boiler combustion is analyzed by static search method.Because the static optimization does not consider the dynamic characteristics of the boiler,the search time is long and the oscillation is easy to occur,so the dynamic optimization algorithm is adopted.There are two basic ways to realize the optimal control method,one is to directly search the optimal state on the object,the other is to search on the established mathematical model.The former is adopted in the computer automatic control device for frequency conversion speed regulation of industrial boiler combustion system.Its advantage is that it is not necessary to establish an accurate mathematical model(it is extremely difficult to establish an accurate mathematical model for boiler combustion system control).How to make the system stable near the optimal working point quickly and accurately in the optimization implementation must involve the selection of optimization parameters and the optimization of algorithm.
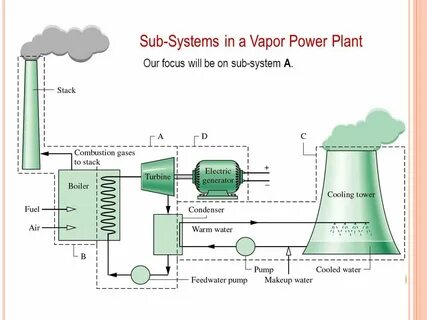
3、Conclusion With the appearance of super large programmable controller,the development of high-speed computing components and the application of intelligent controller,the boiler control system will realize completely unattended automatic control.
More...
PLC-Module.com | XiongBa Industrial Control | Panda | Computer control system for industrial boiler |